Air spiral systems for
pasteurizing
cooling and
freezing
pasteurizing
cooling and
freezing

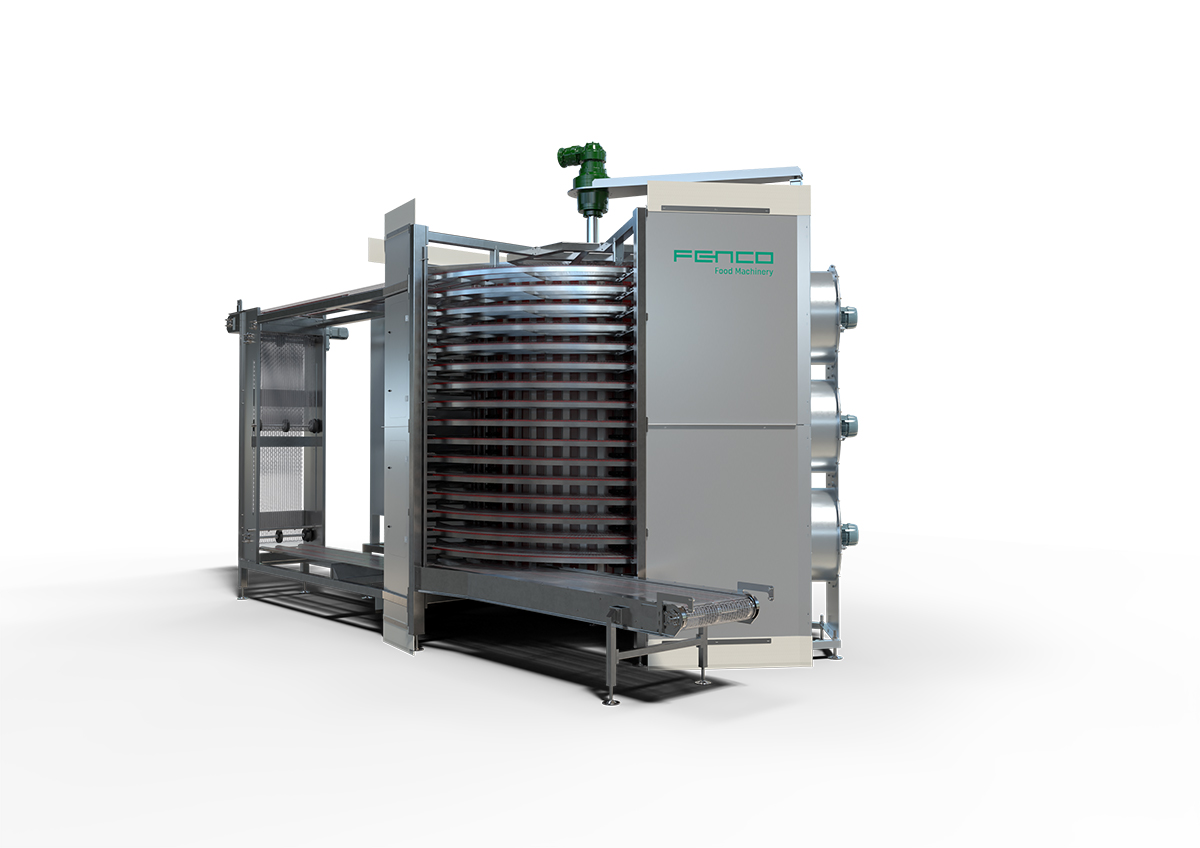
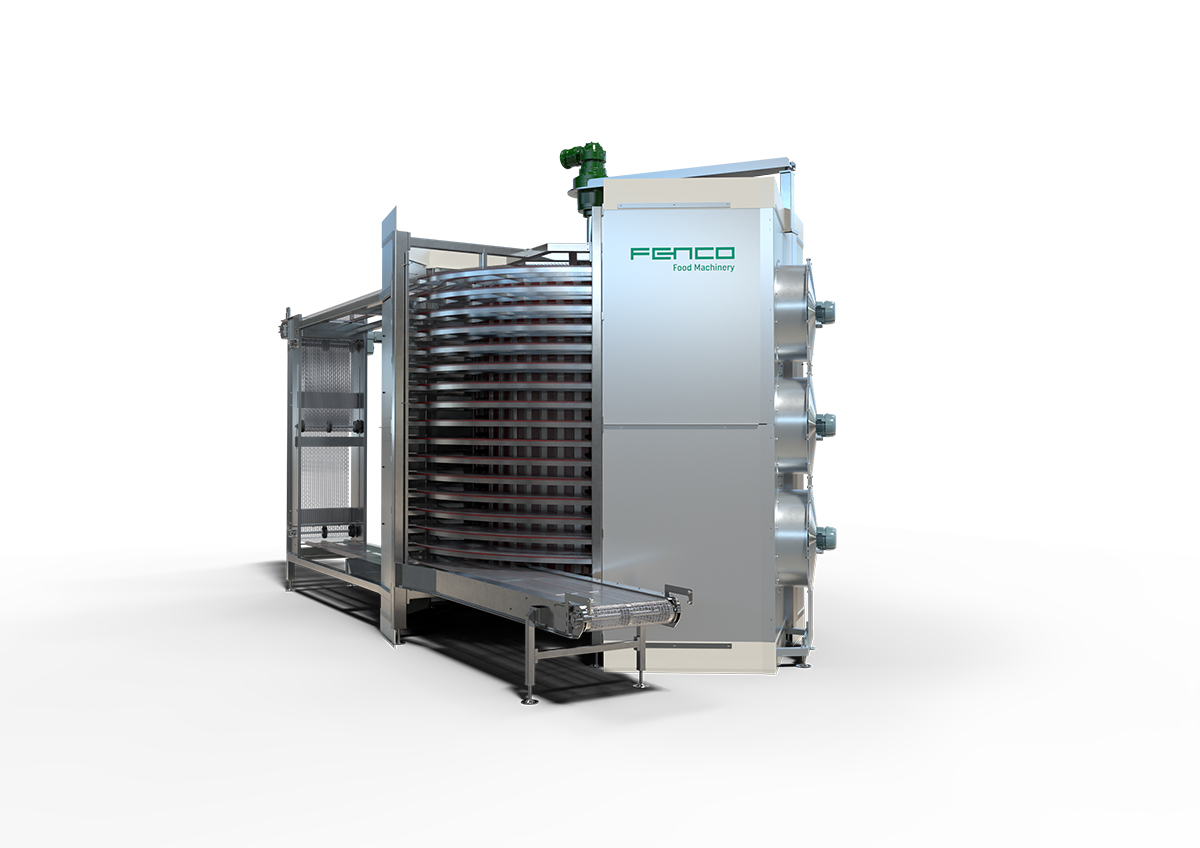
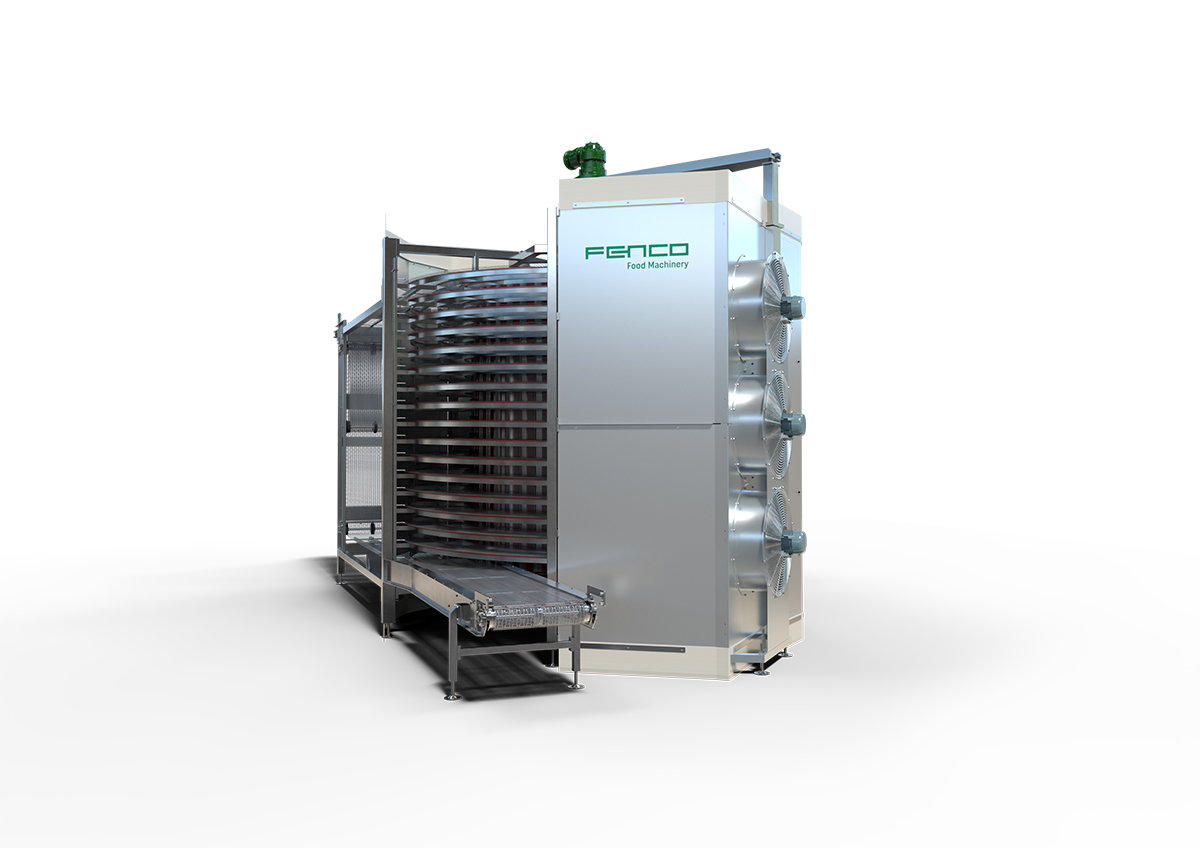
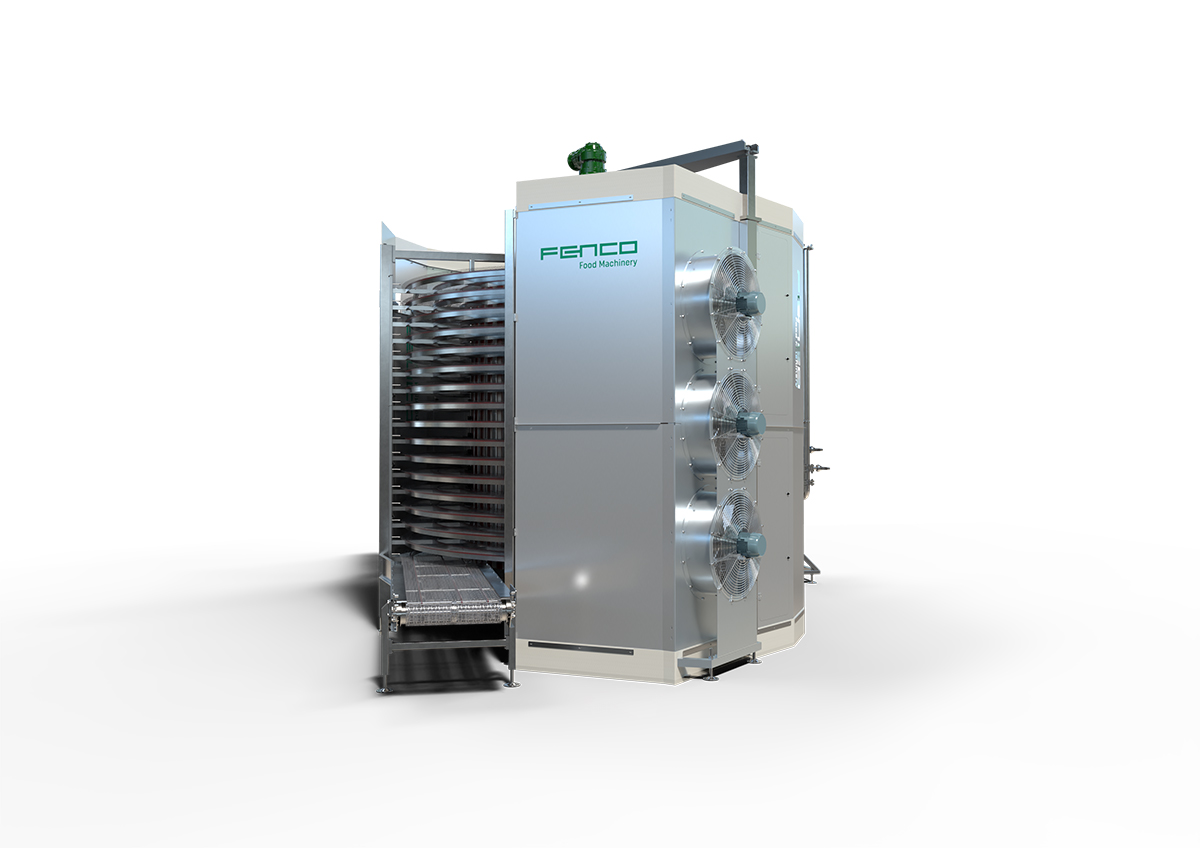

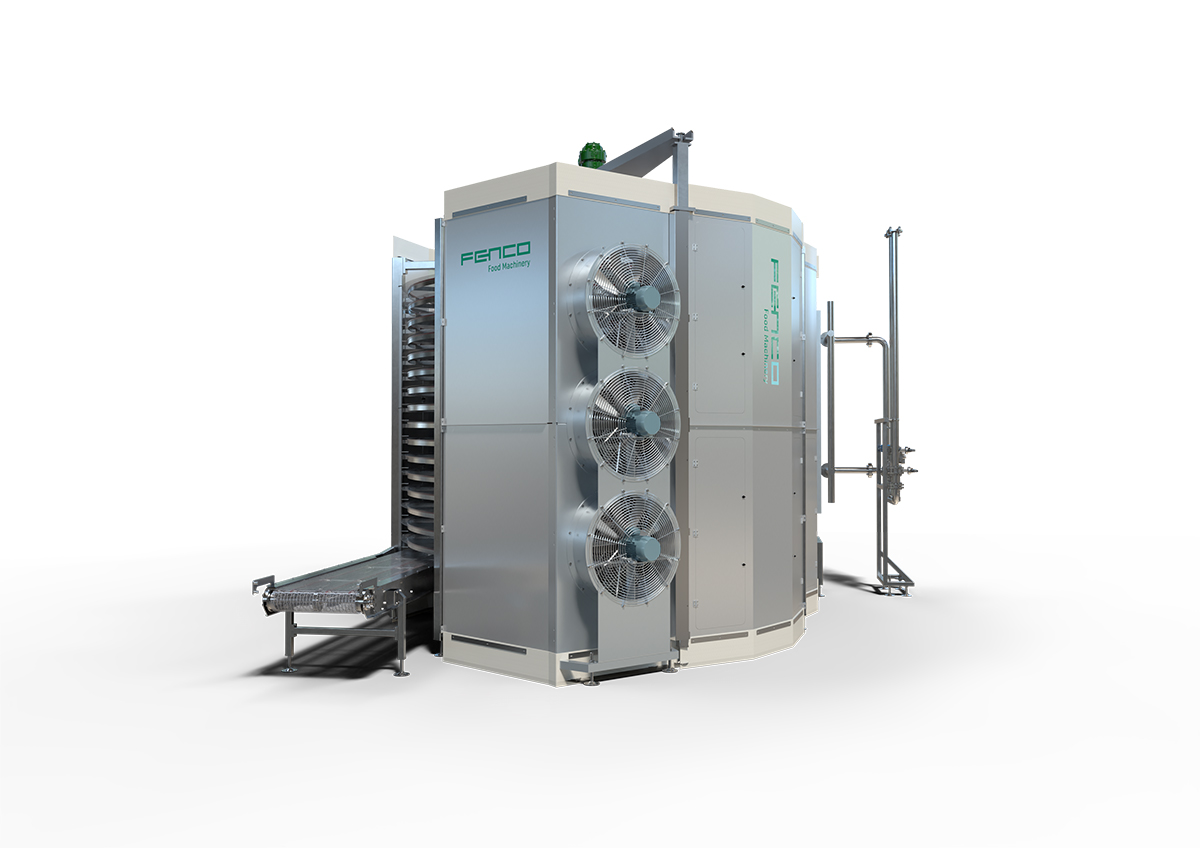
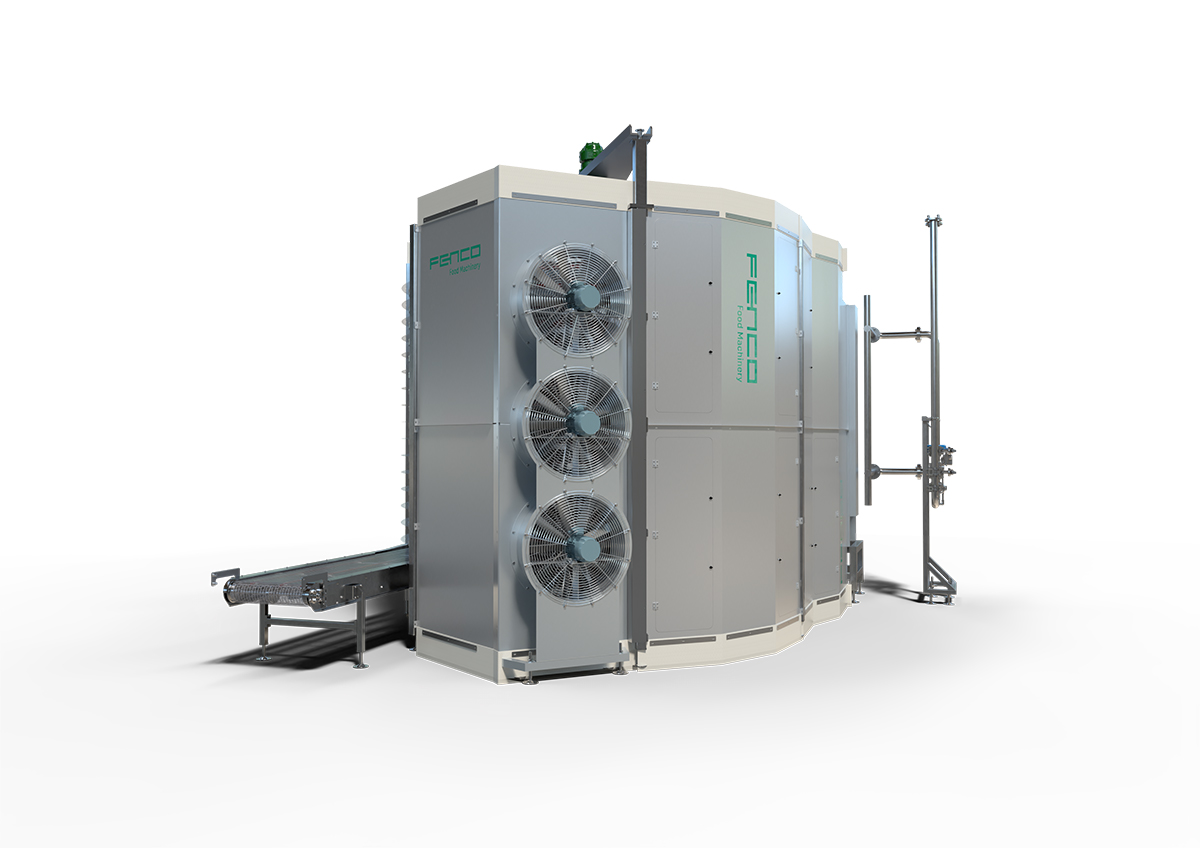
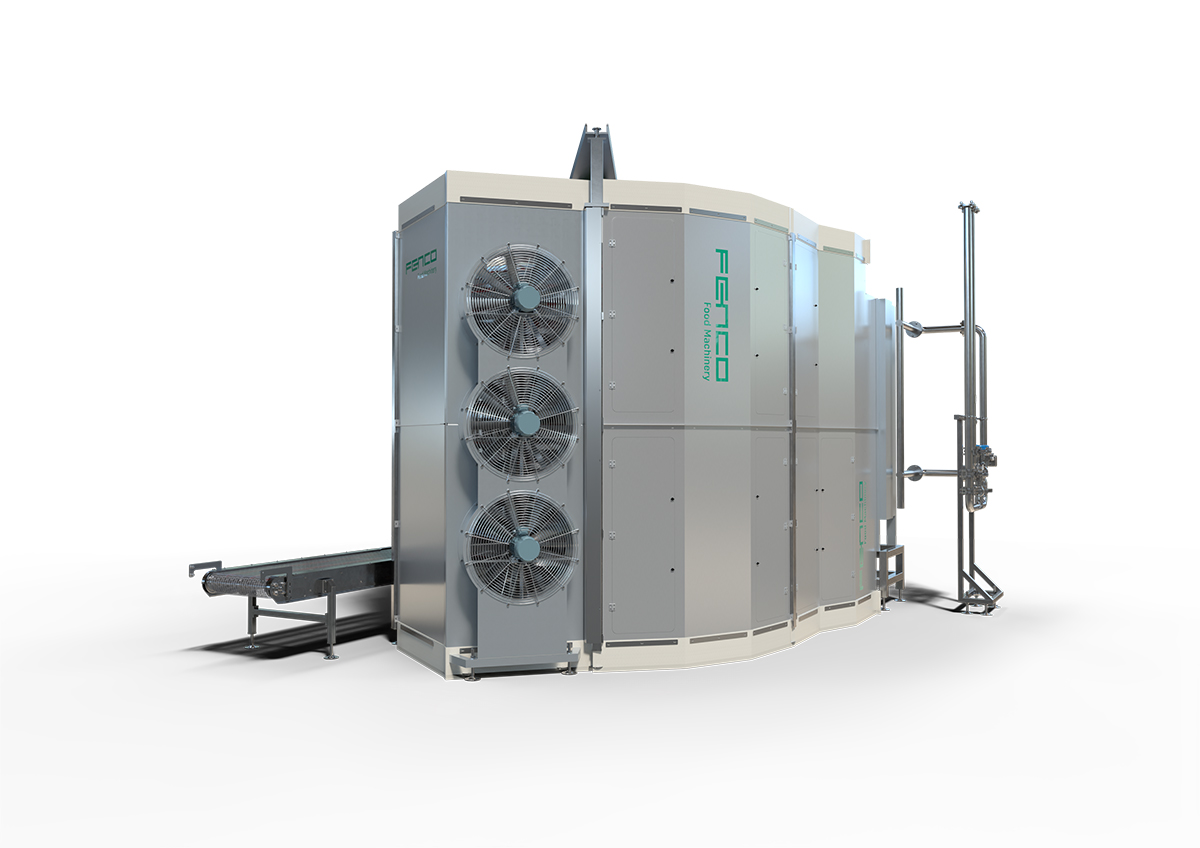
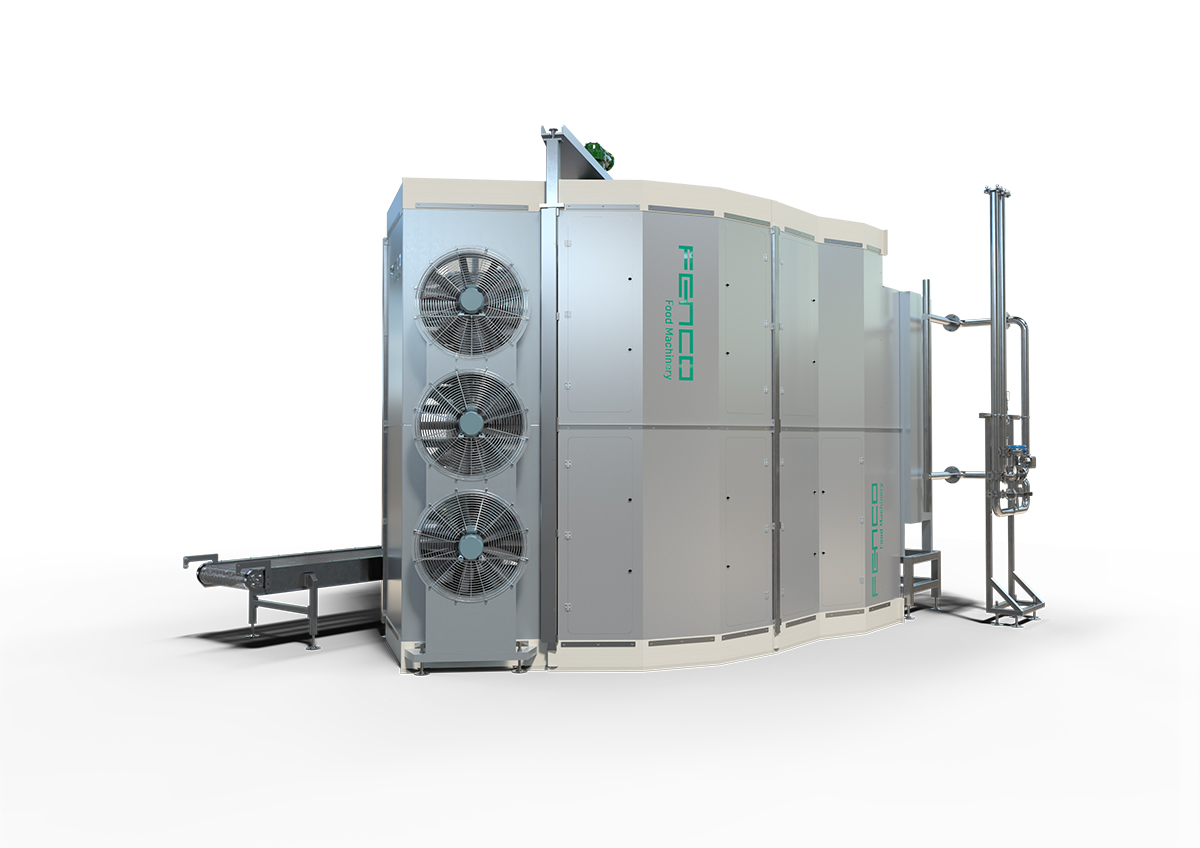

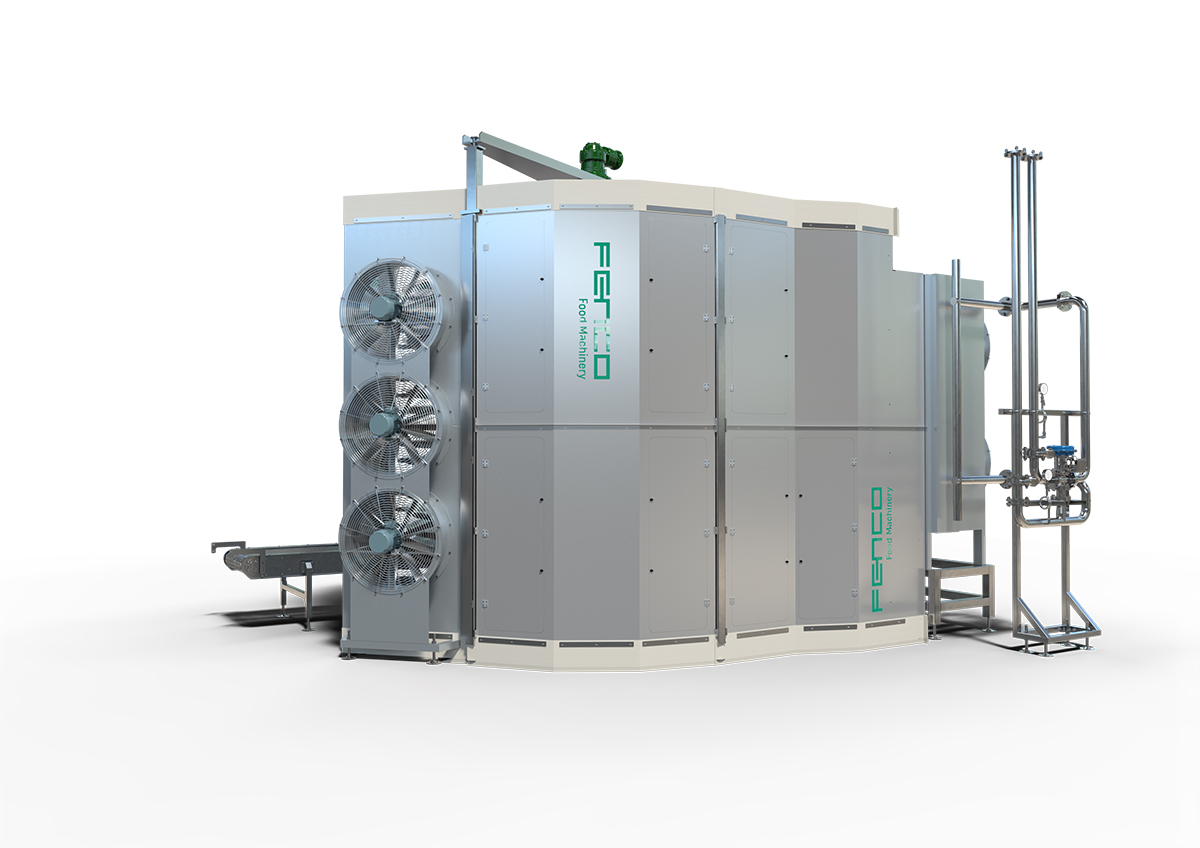
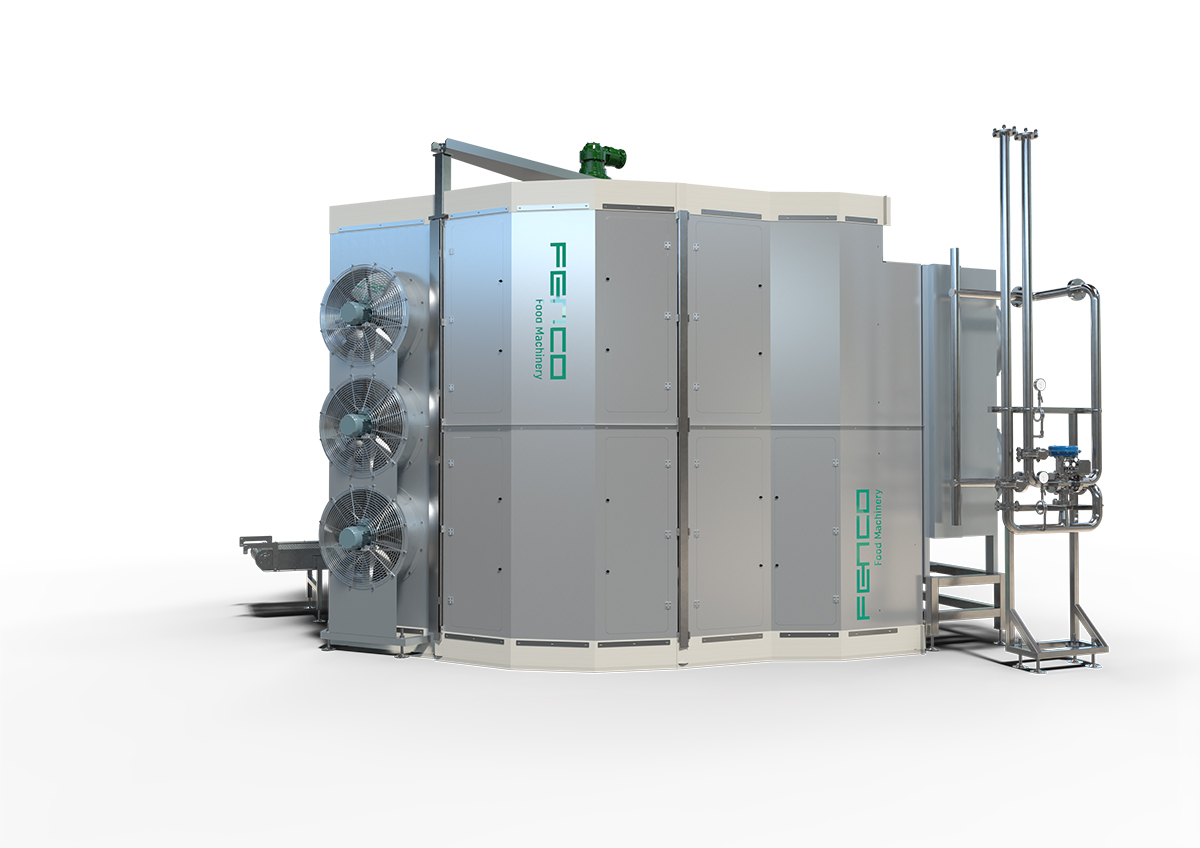
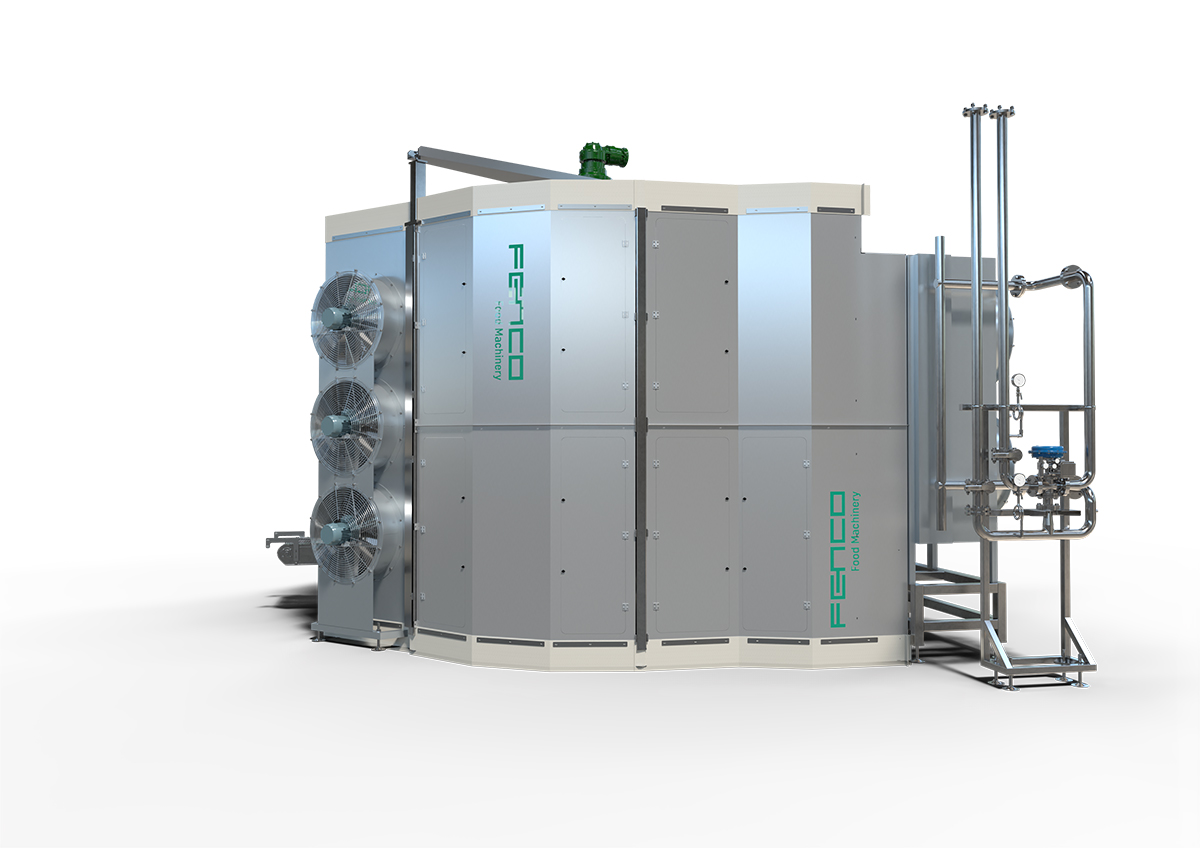
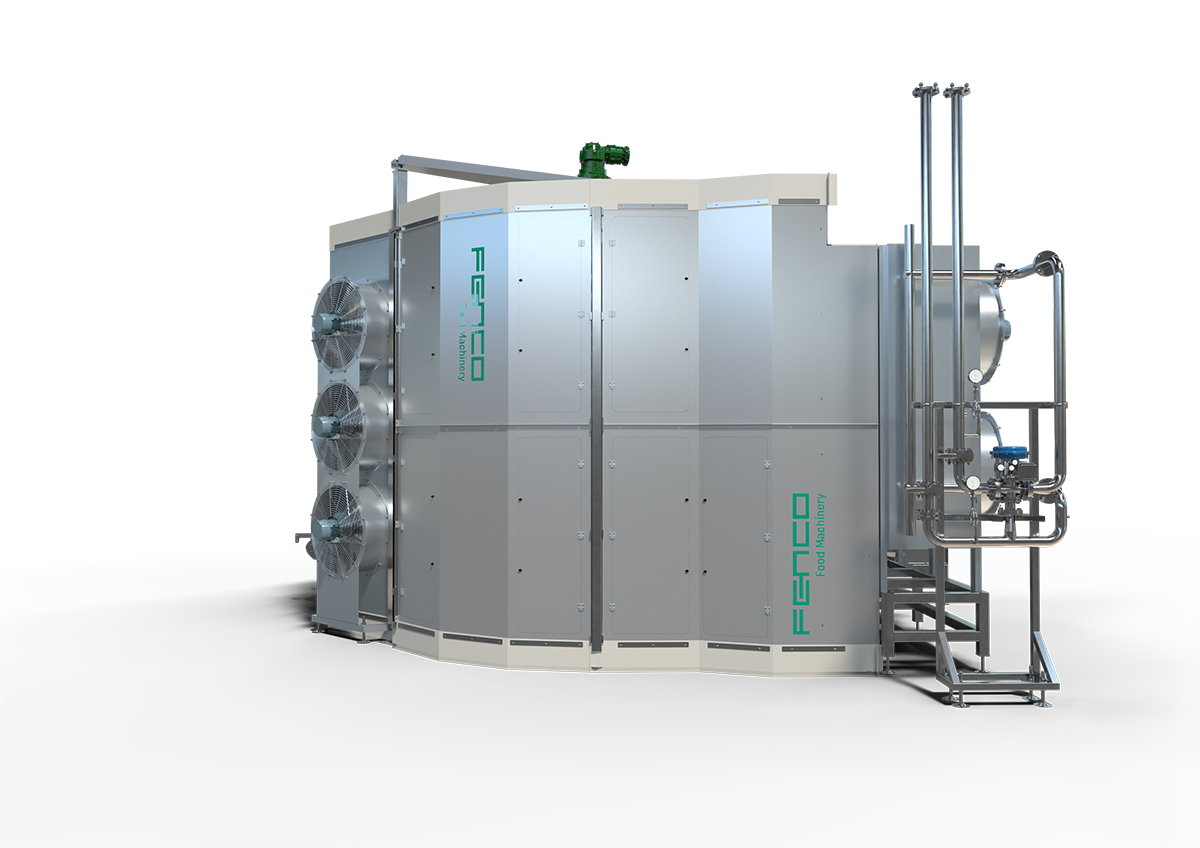
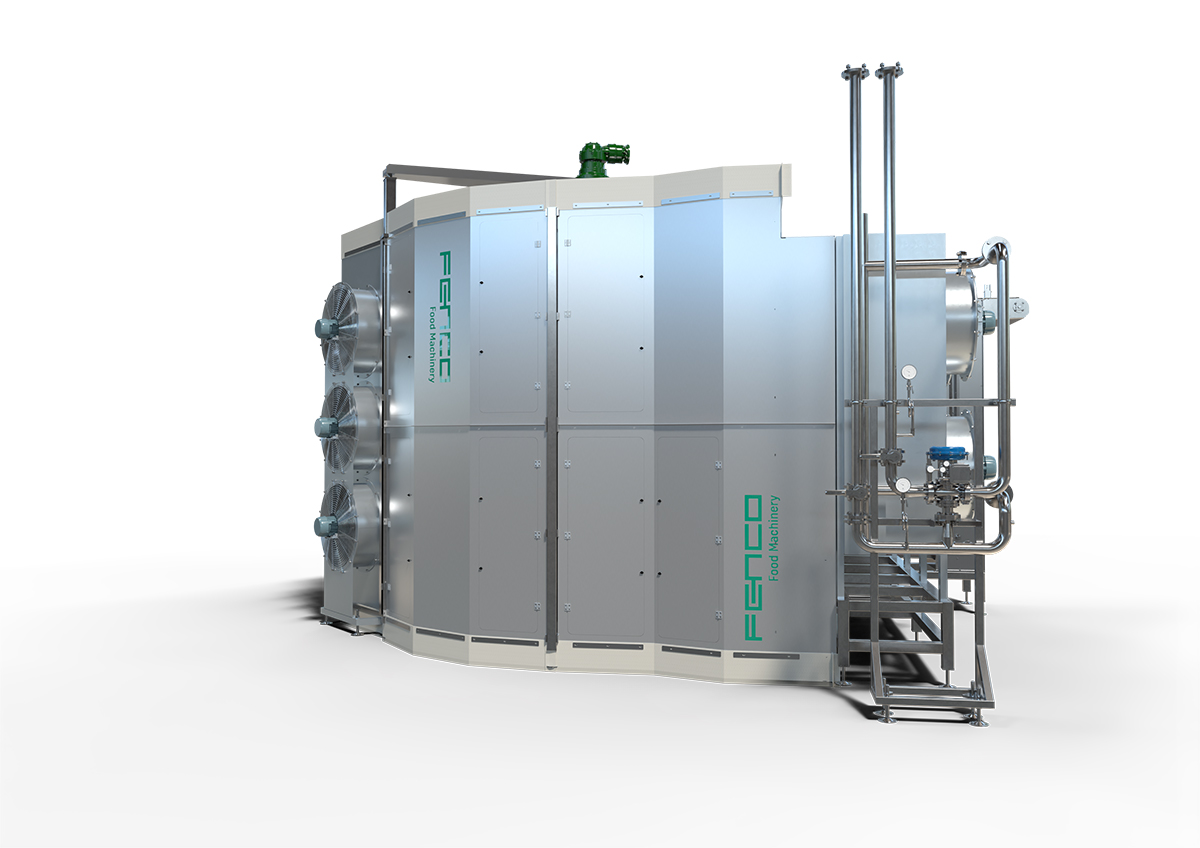
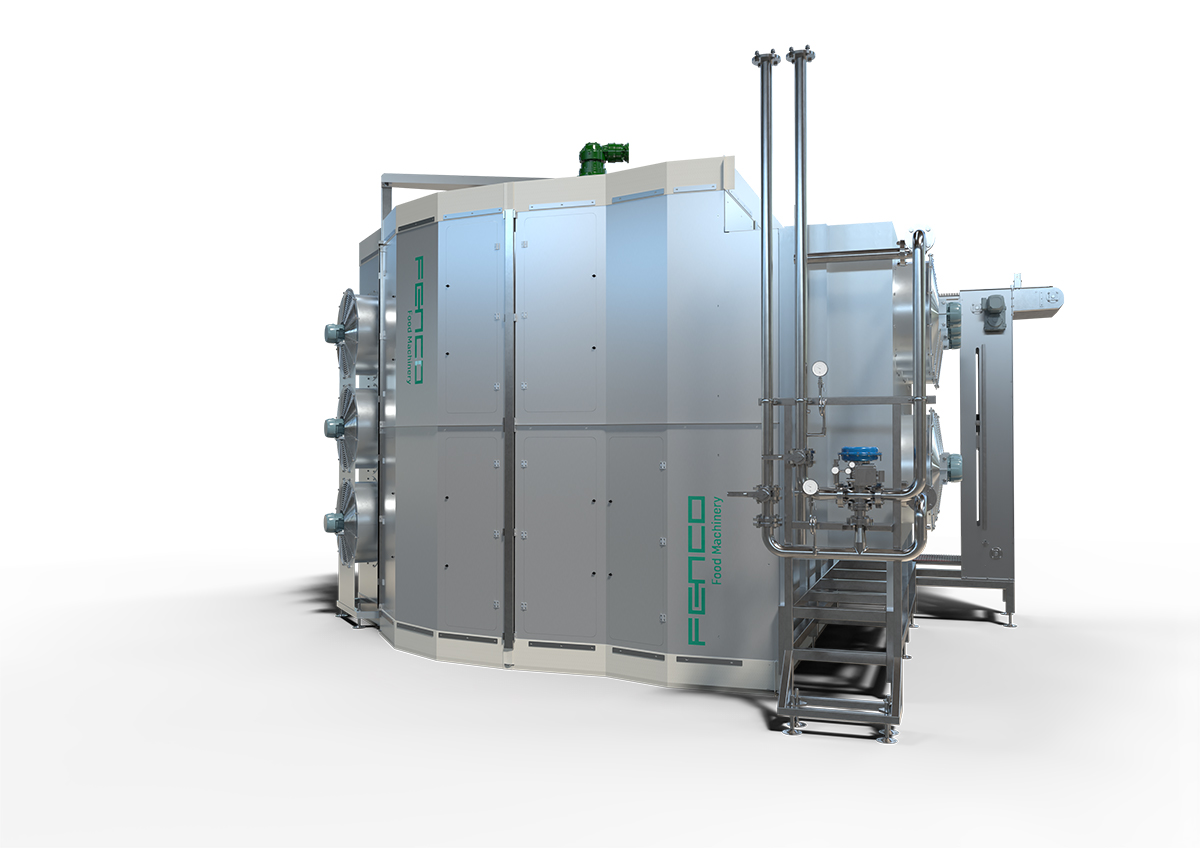

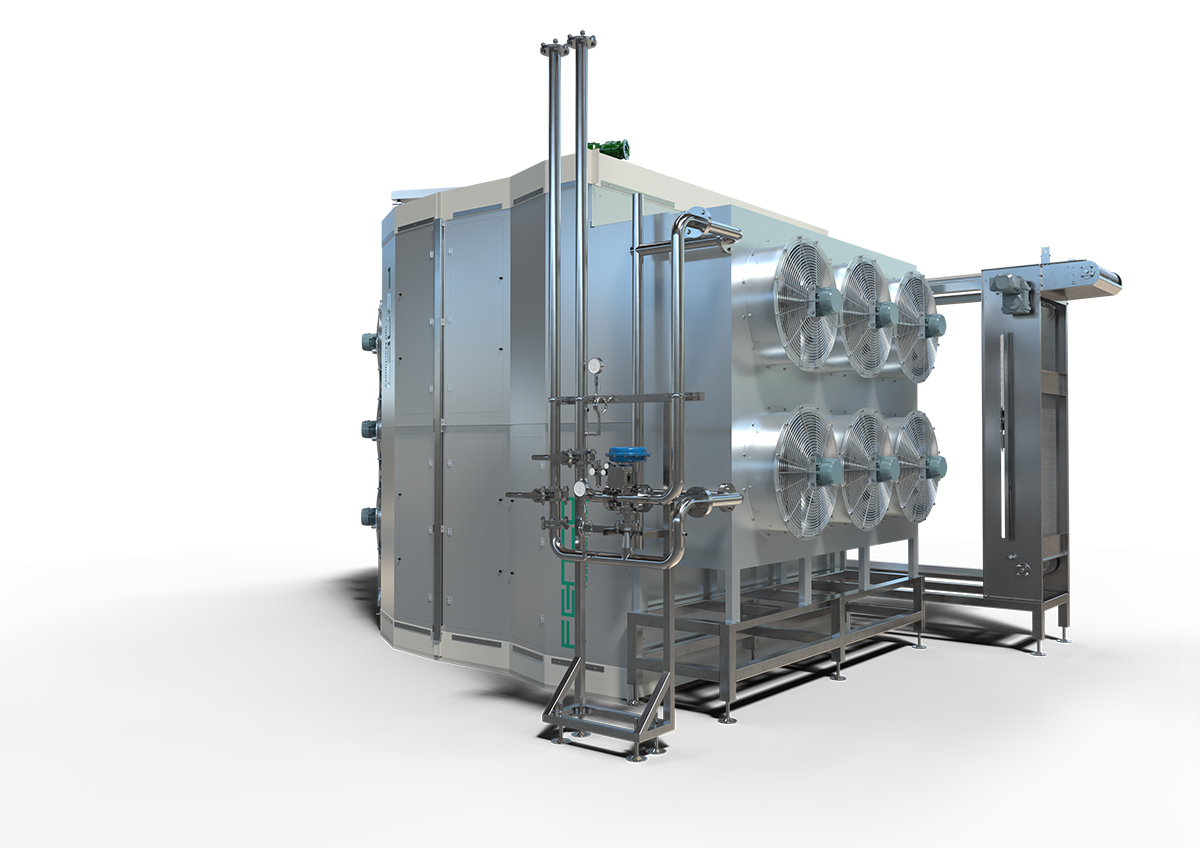
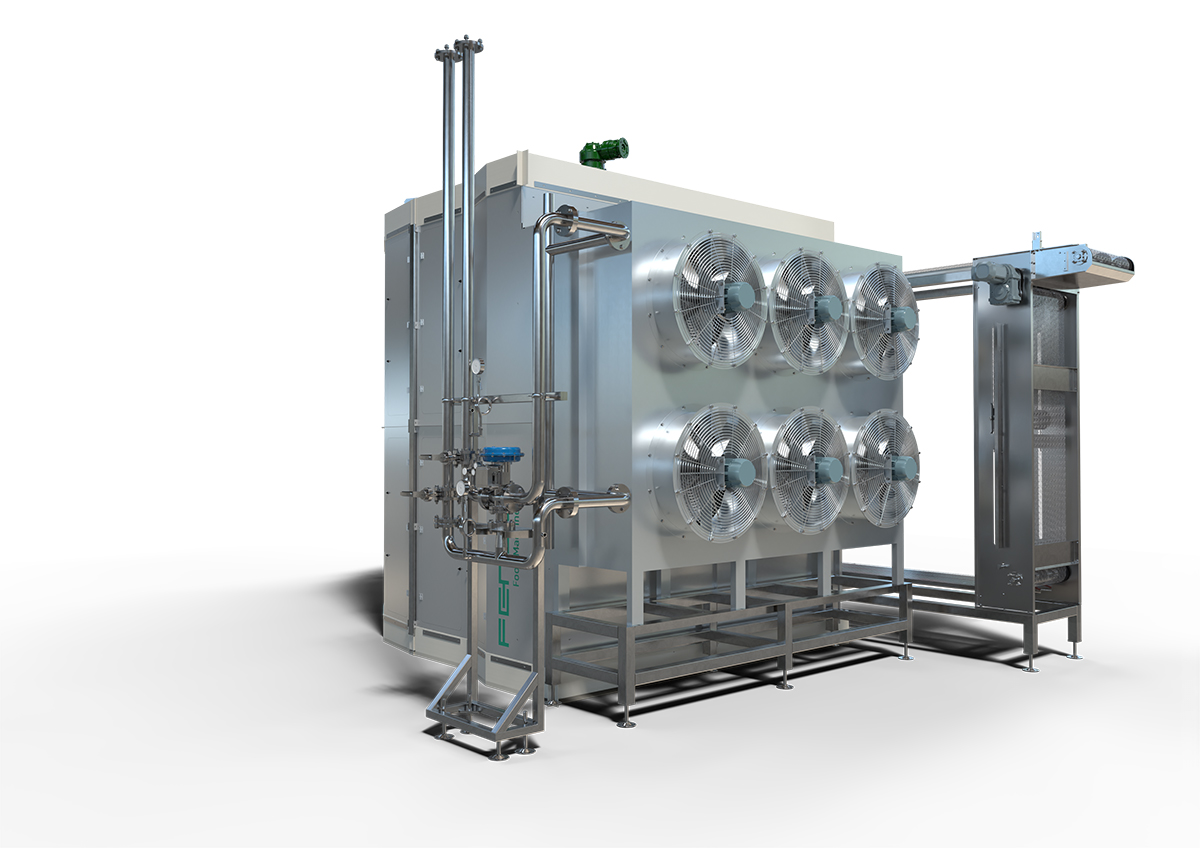
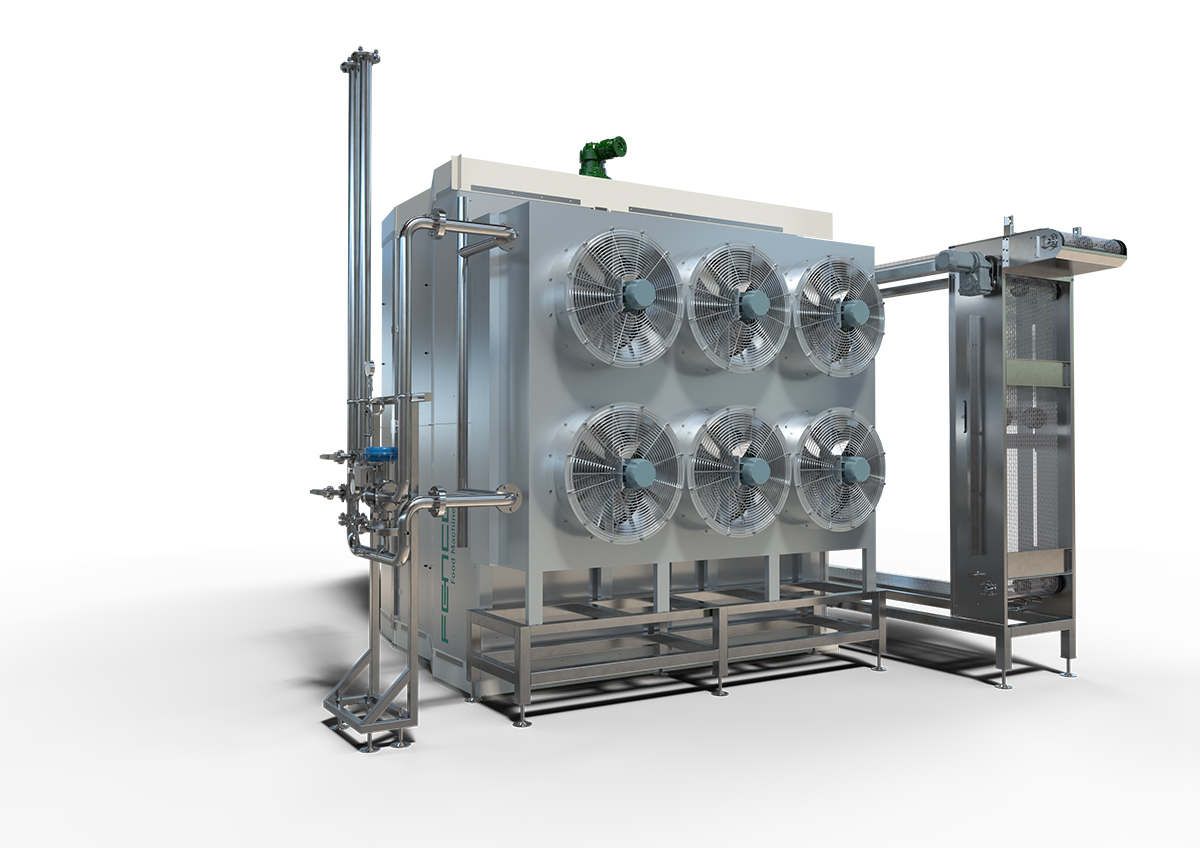
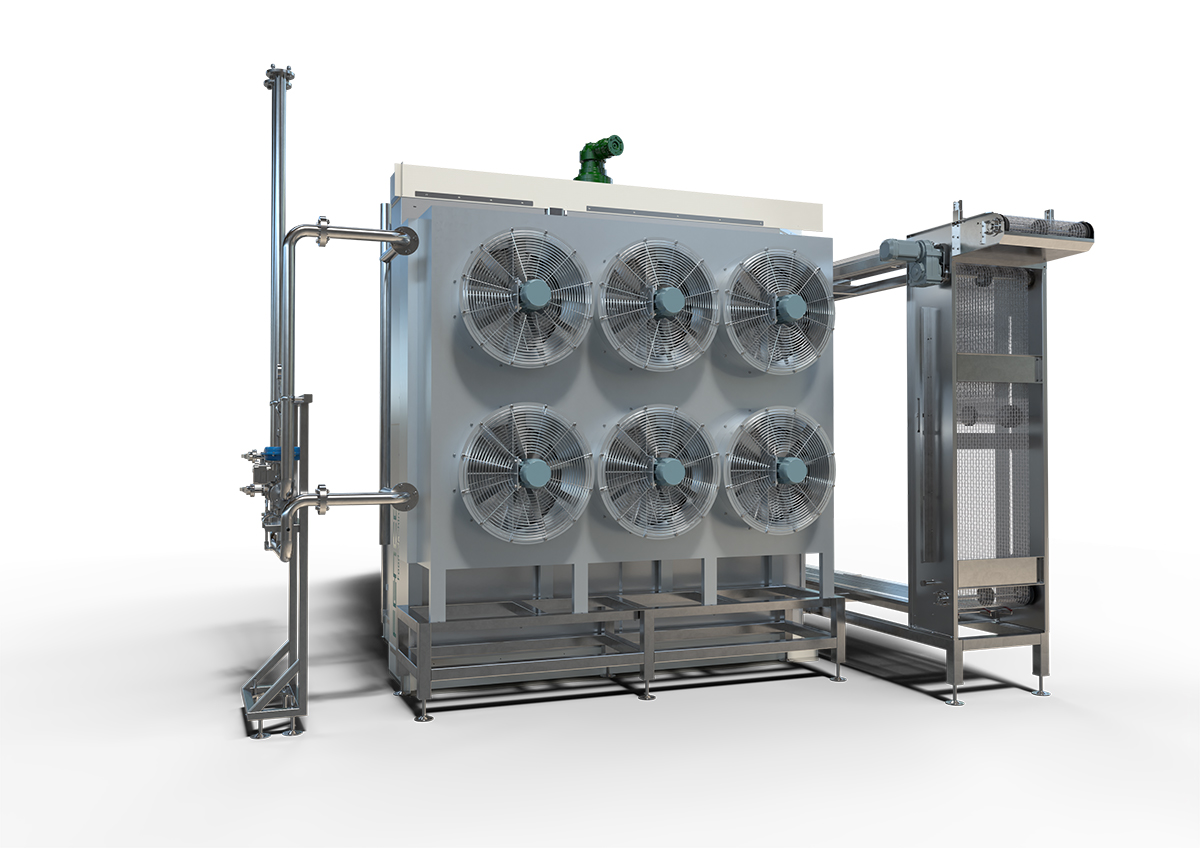
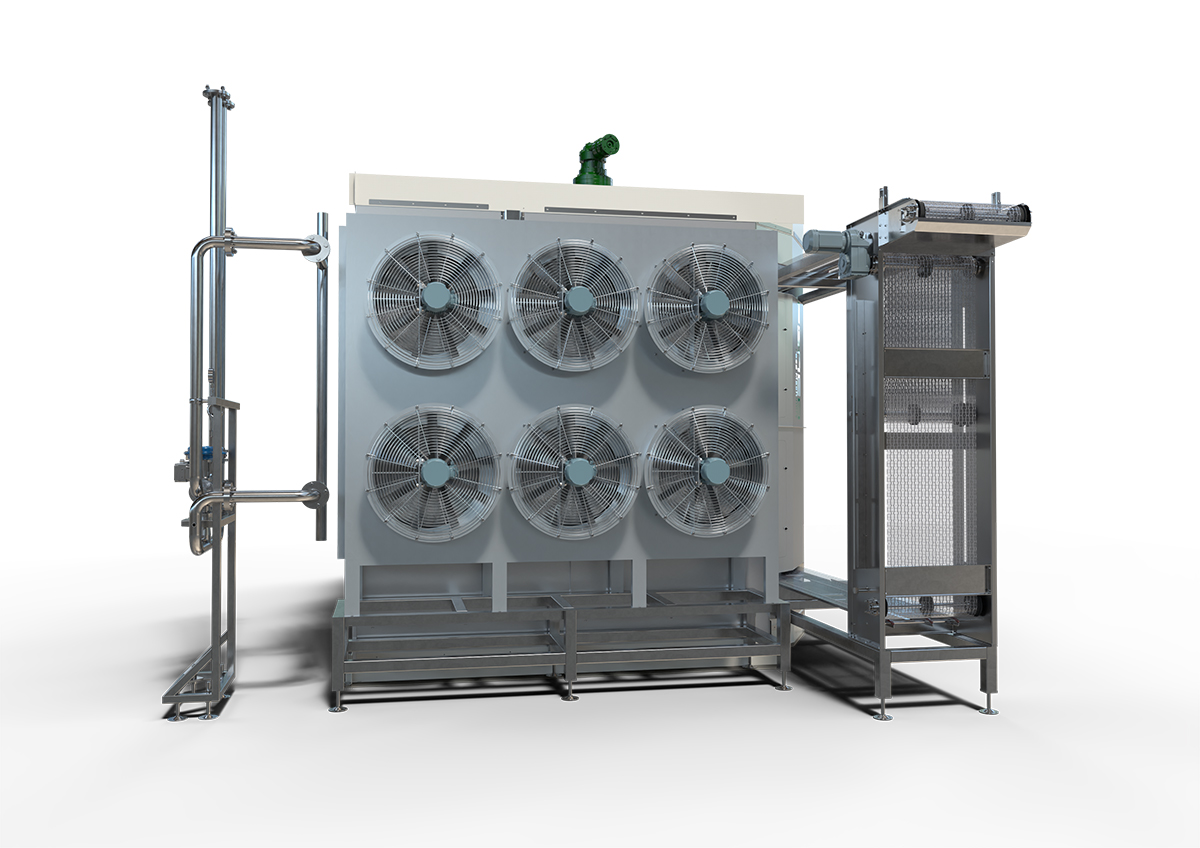
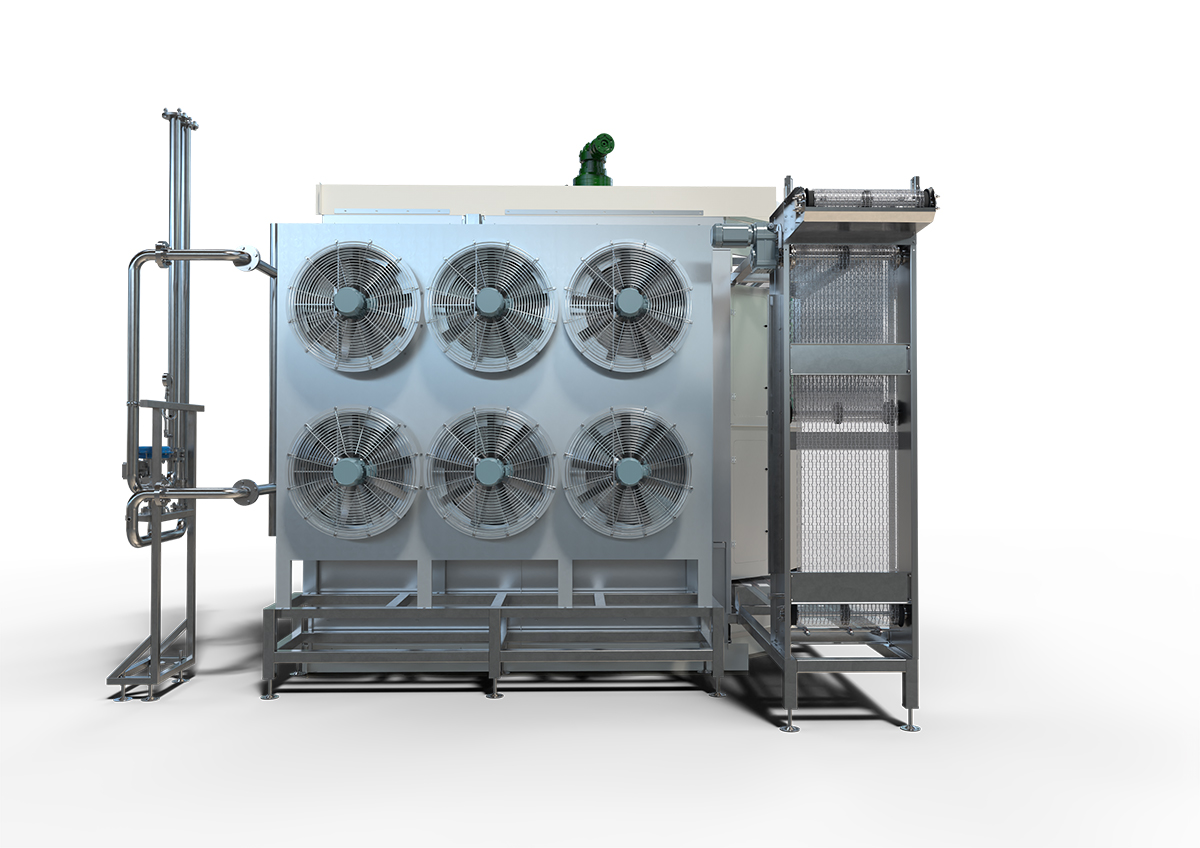
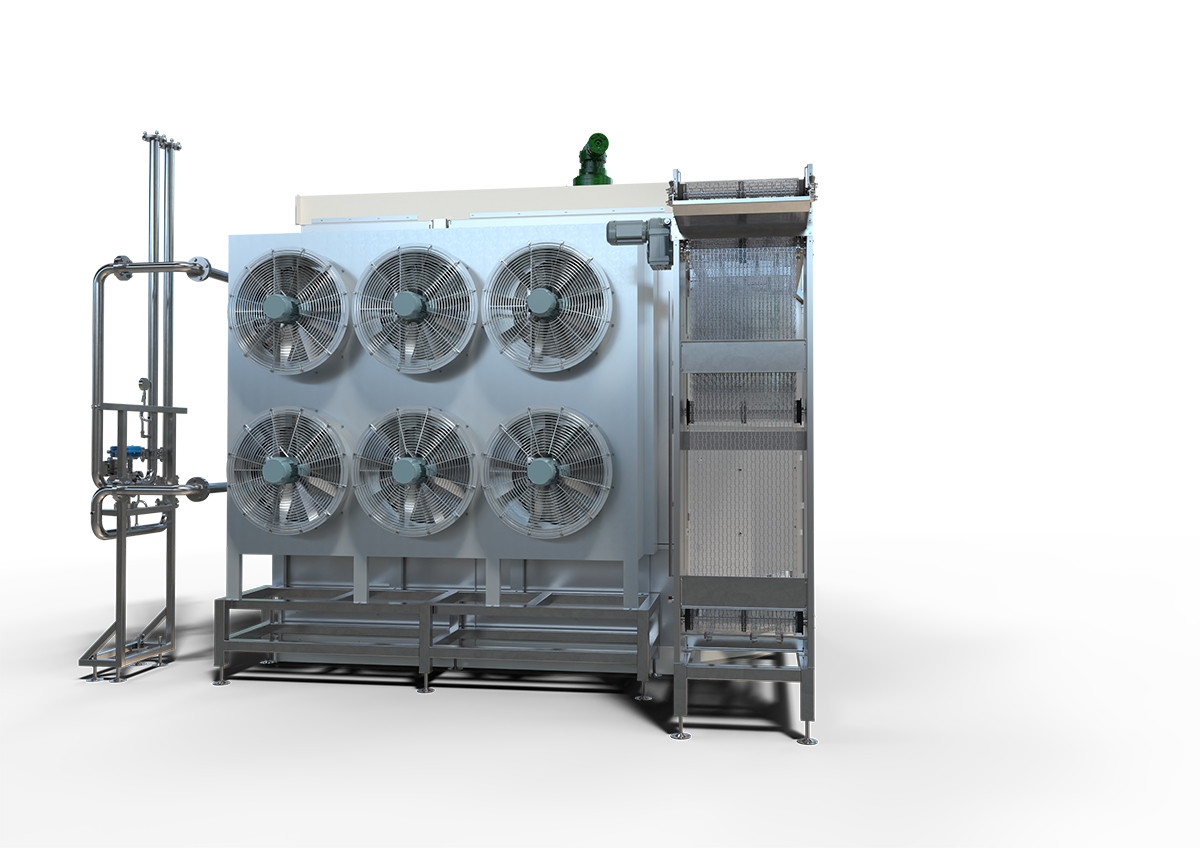
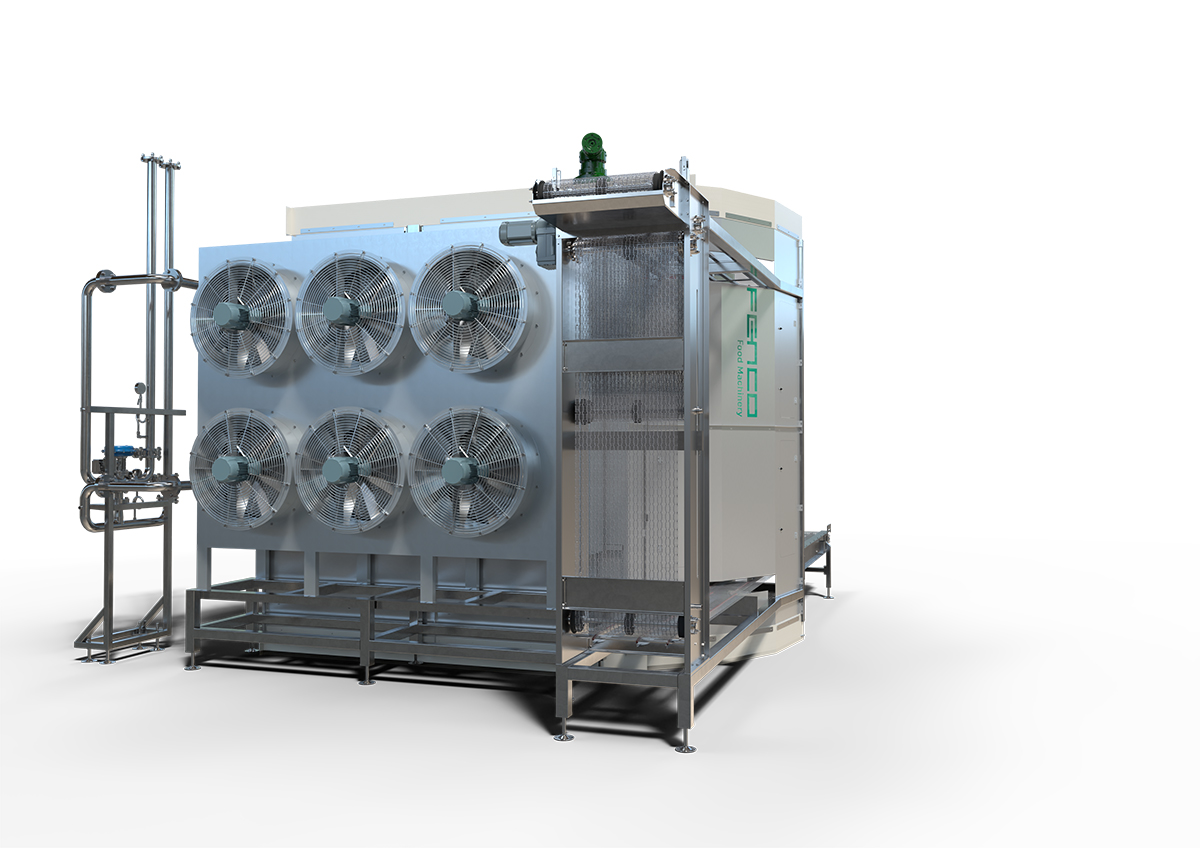
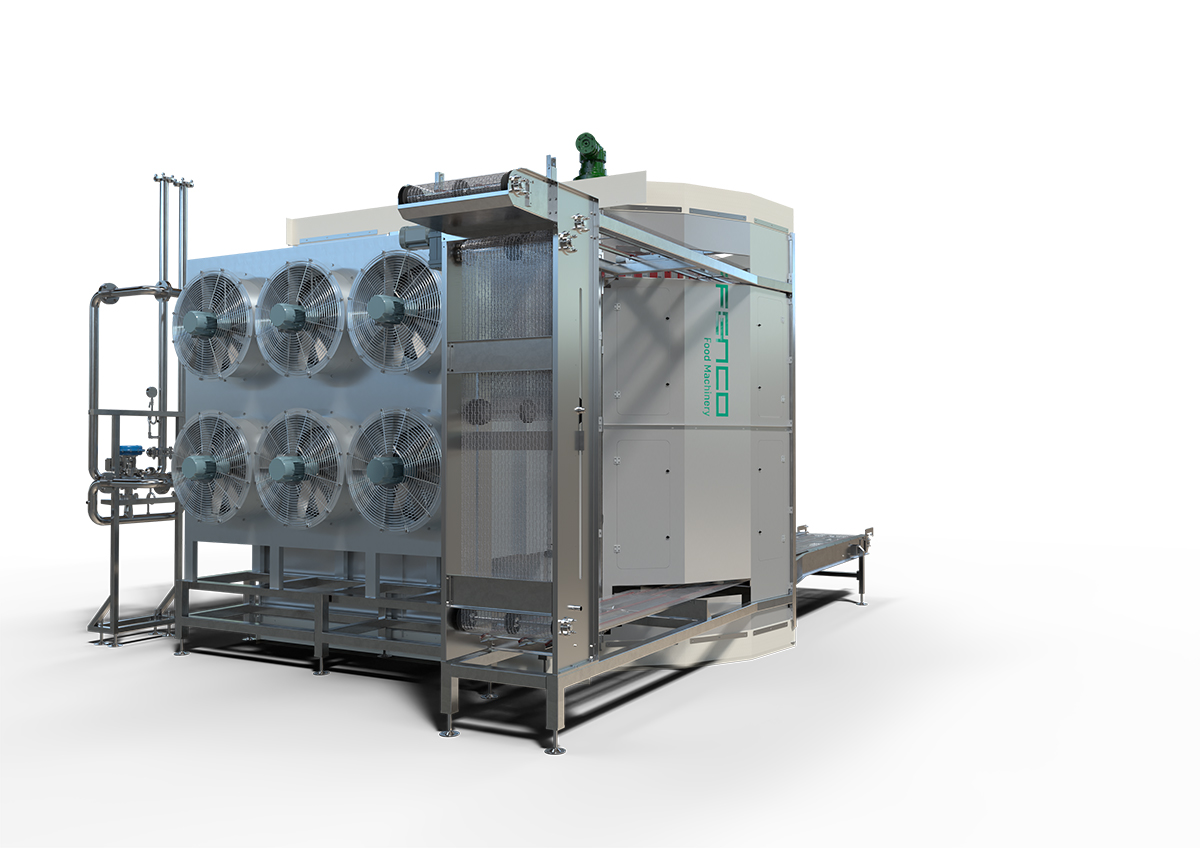
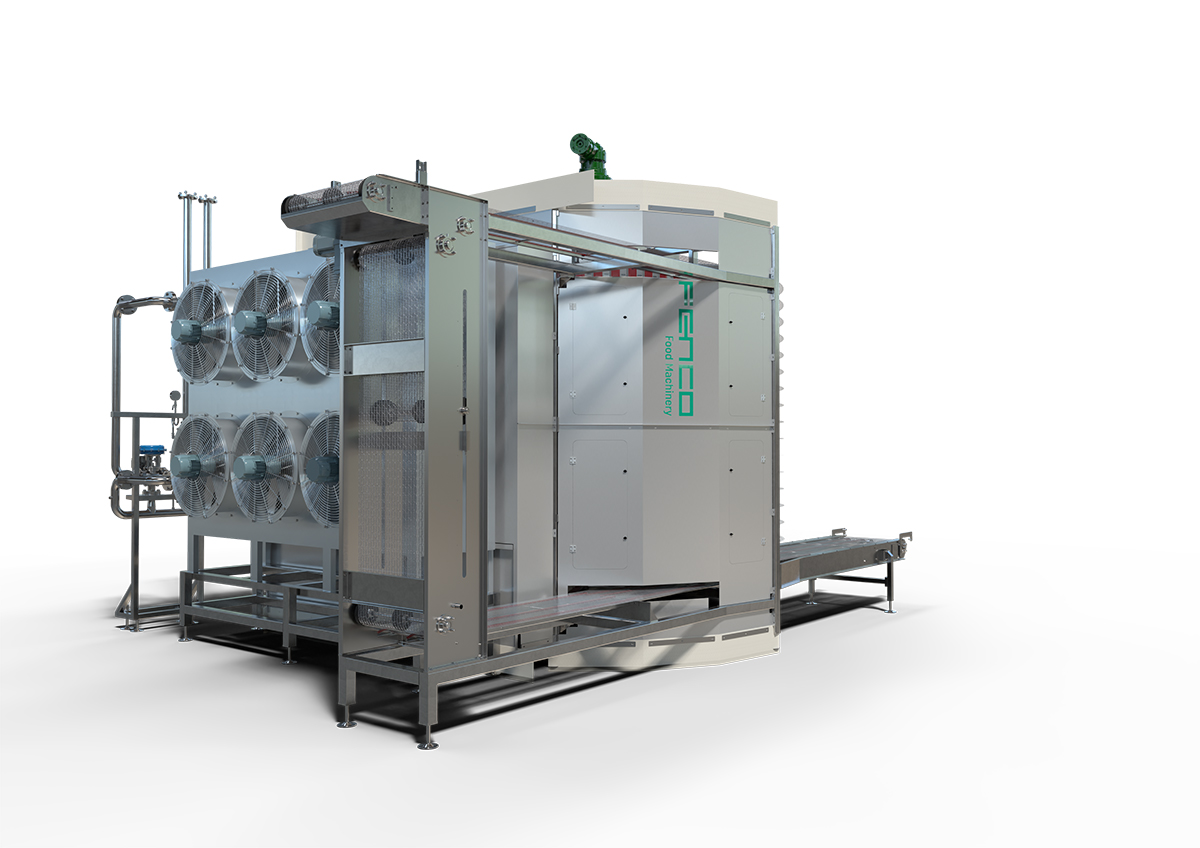
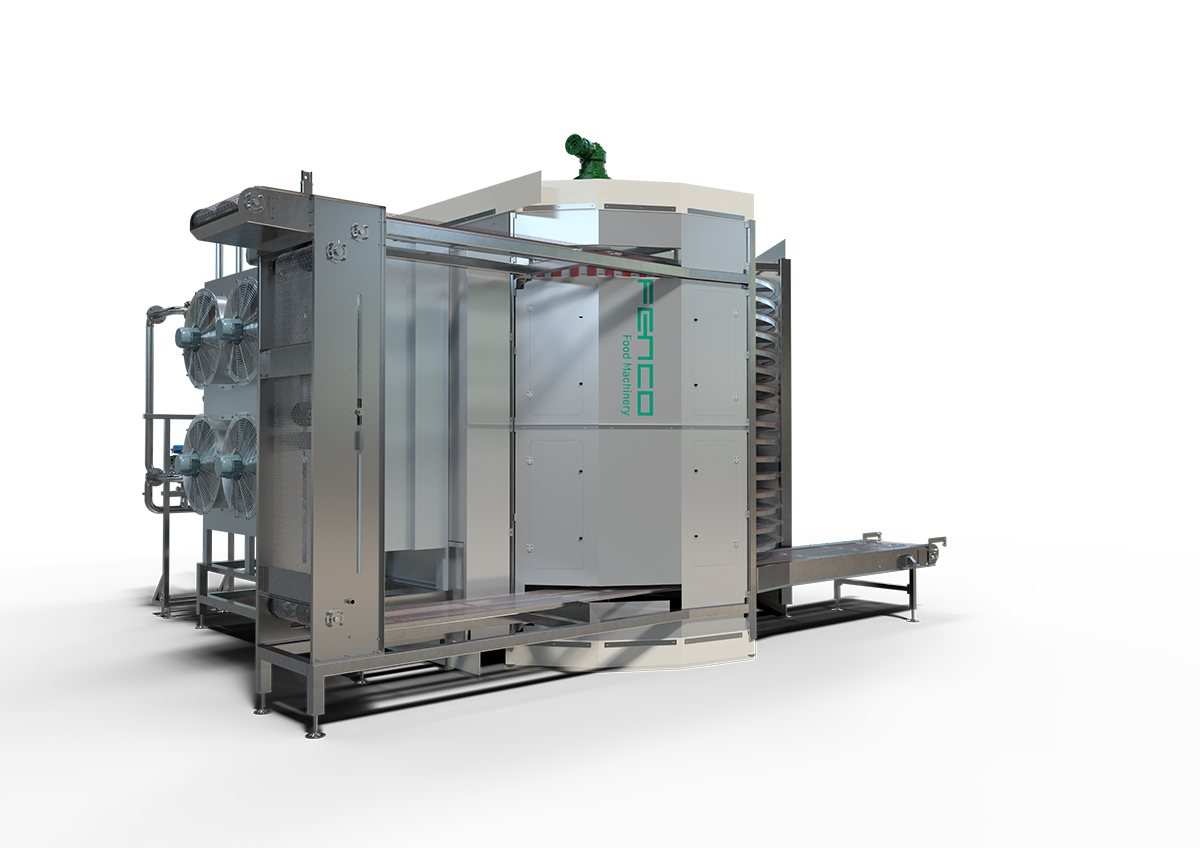
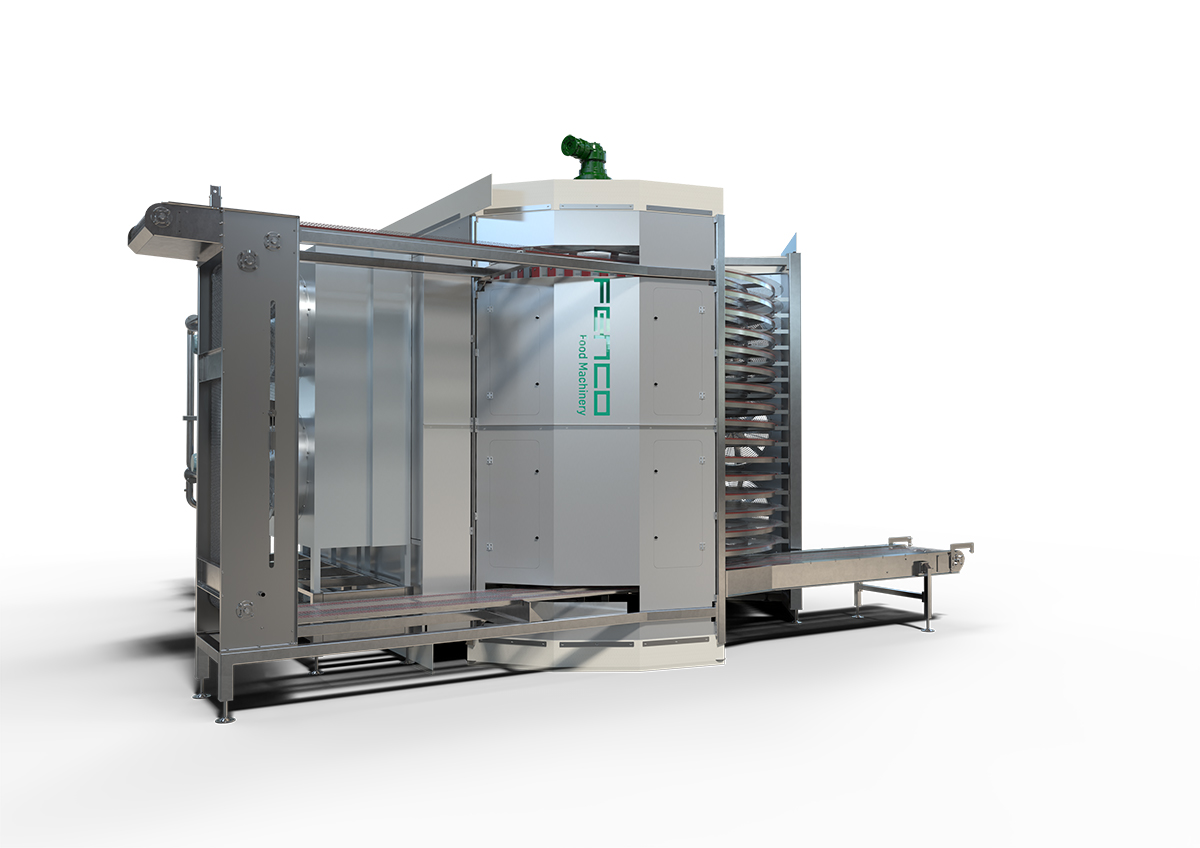
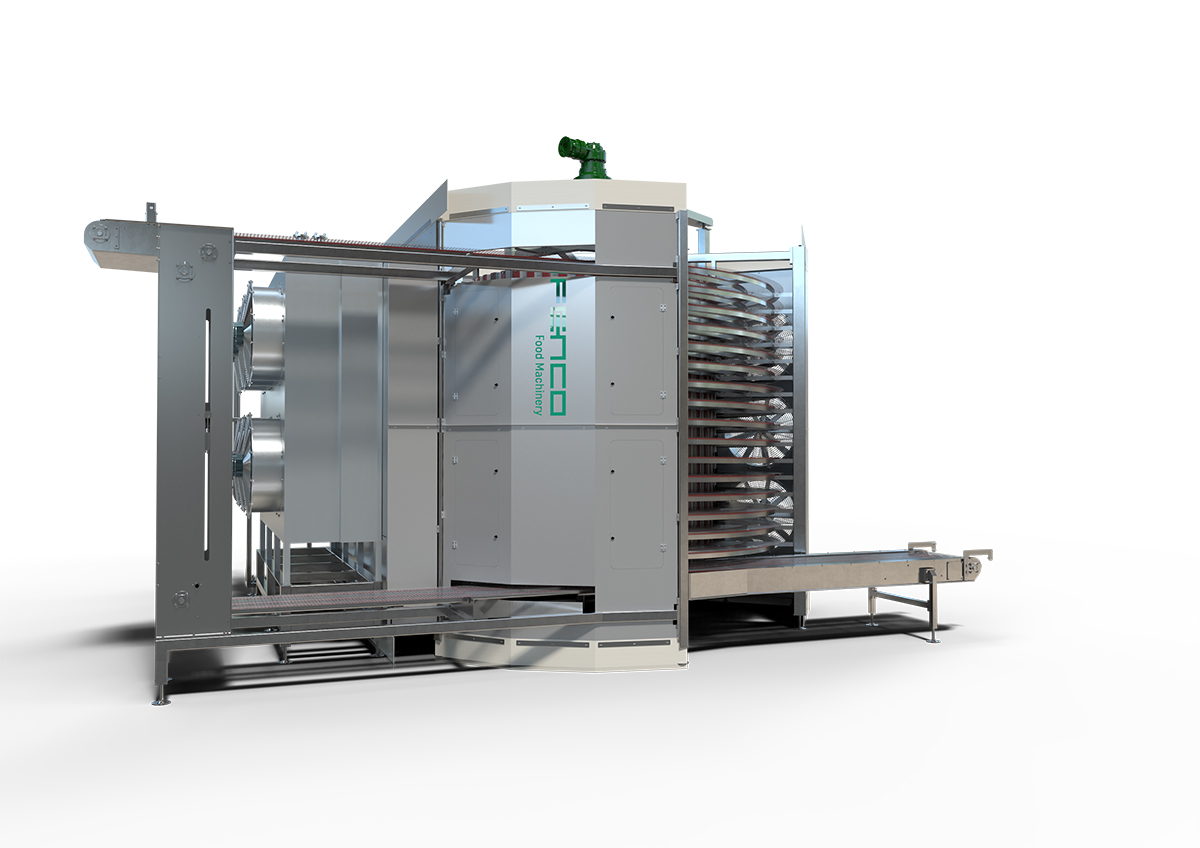
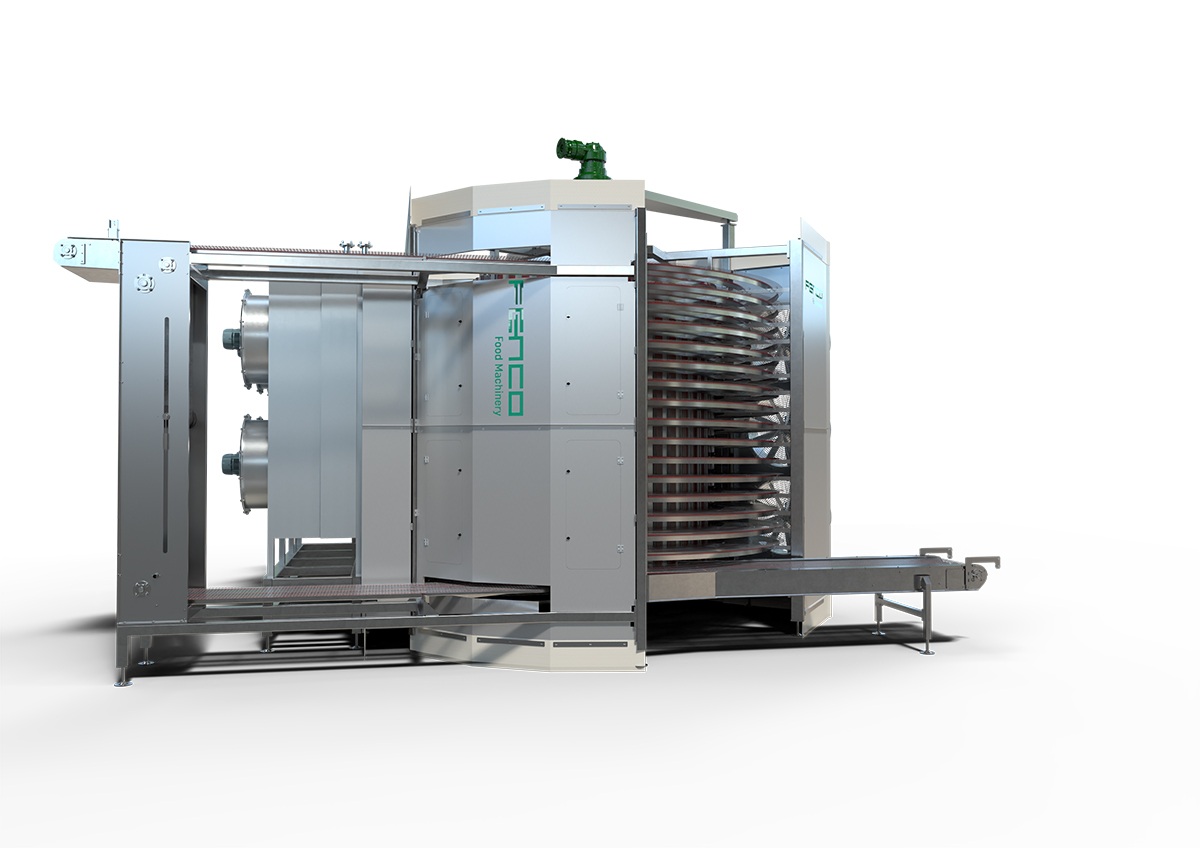
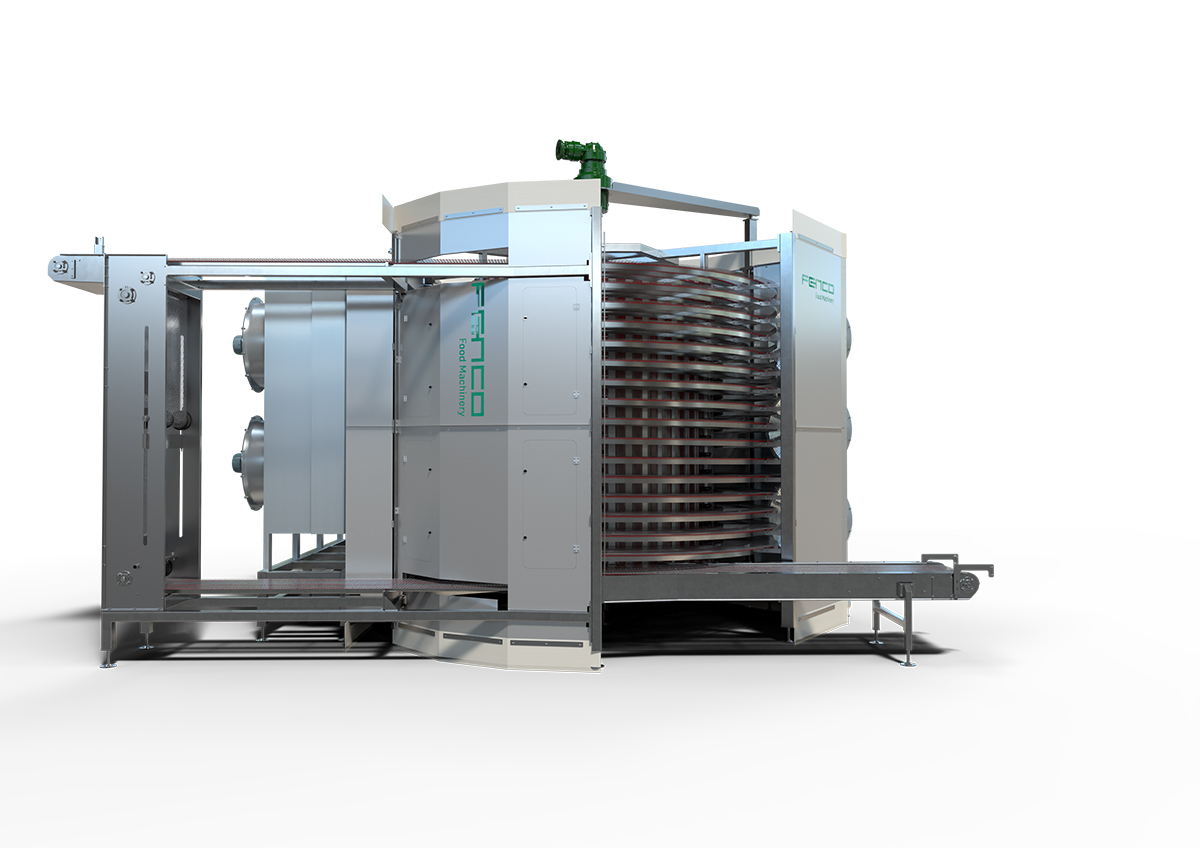
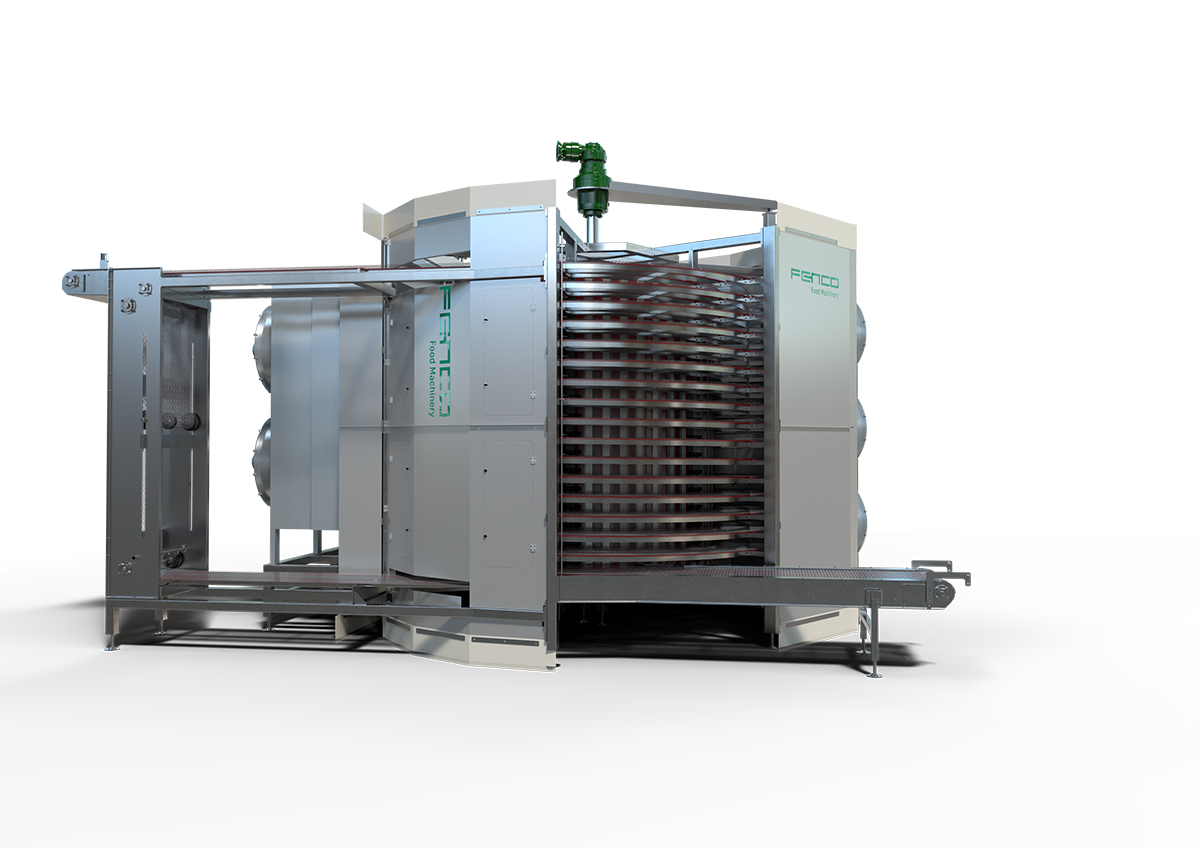
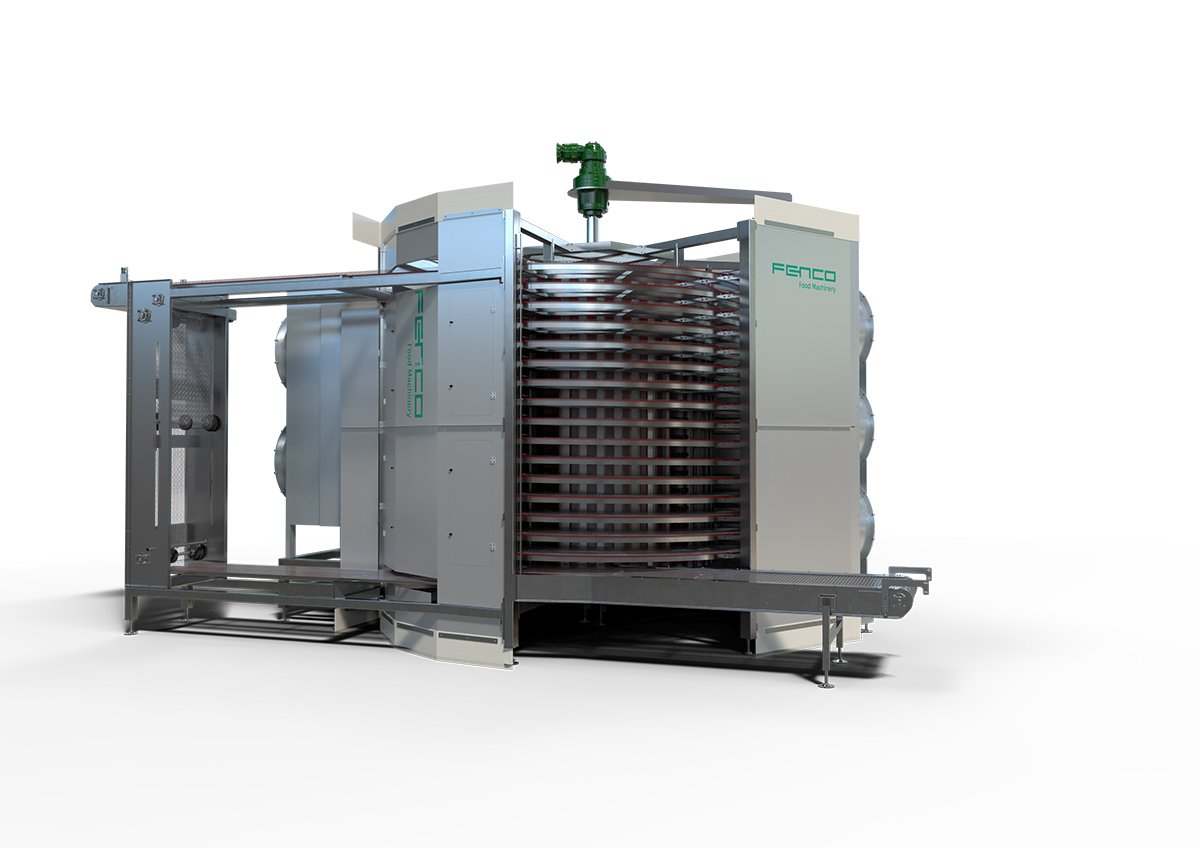
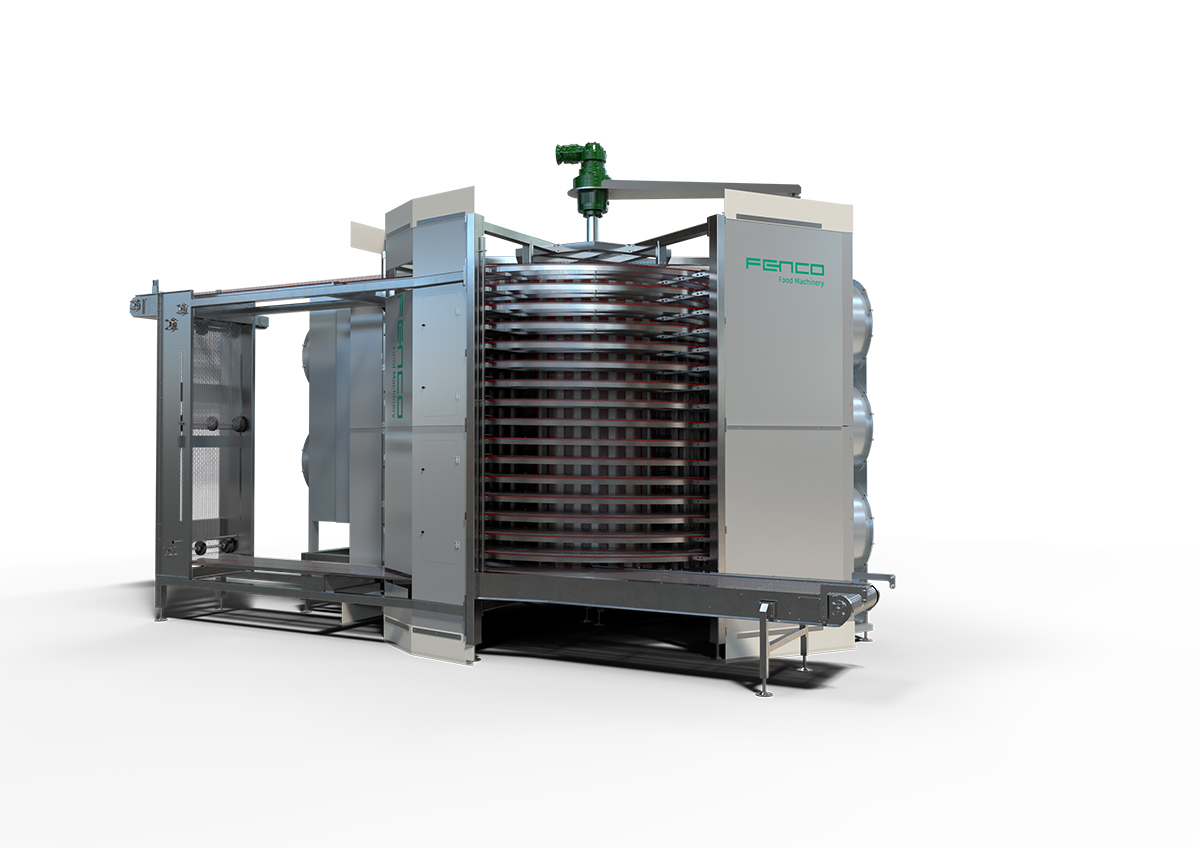
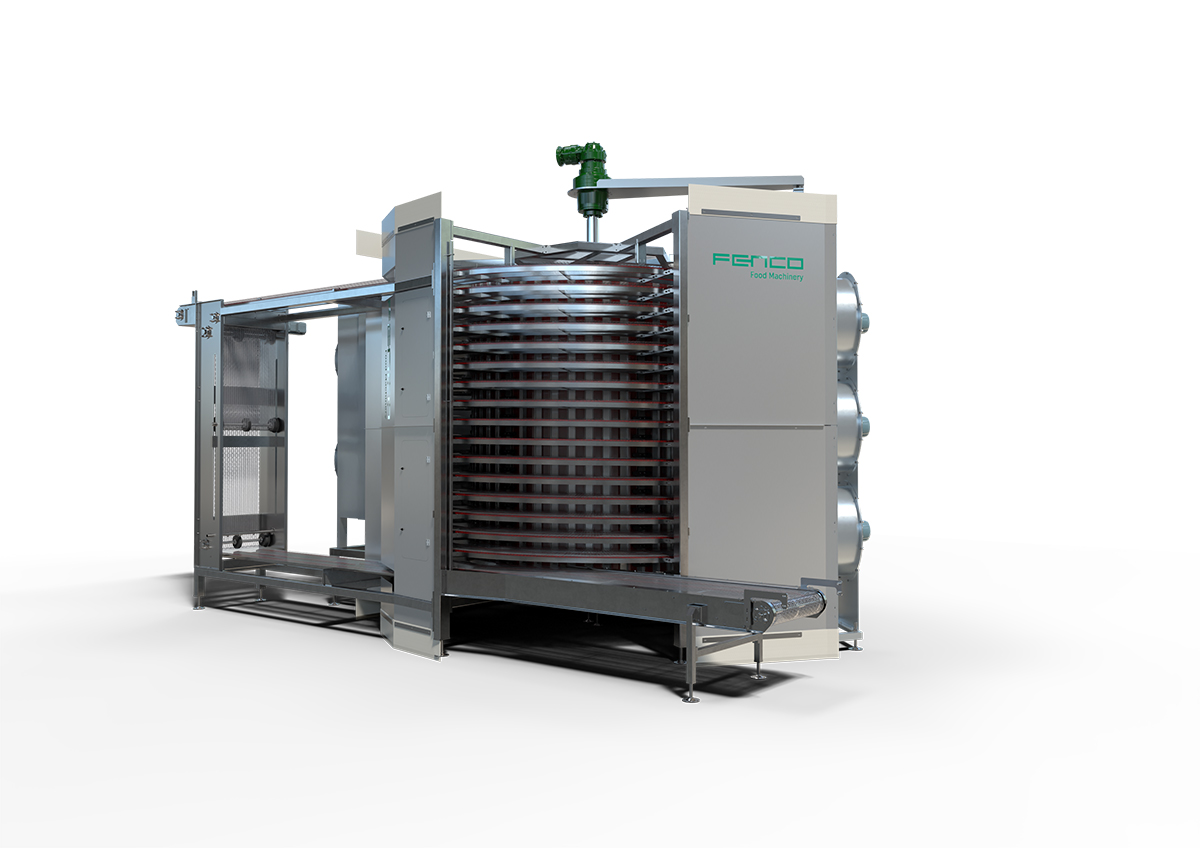
The air solution is preferable for small packages. In this way, the need for drying of the containers is avoided.
Moreover, this solution is necessary in case of unpackaged products.
TAP & TAC is the spiral pasteurization (TAP) and air-cooling (TAC) solution alternative to the traditional water pasteurization and cooling line. It is particularly appropriate in the following cases:
- water is not available or is too expensive;
- in the case of very dry environments, where water can create problems for production;
- with water-sensitive packaging.
Moreover, this solution is necessary in case of unpackaged products.
TAP & TAC is the spiral pasteurization (TAP) and air-cooling (TAC) solution alternative to the traditional water pasteurization and cooling line. It is particularly appropriate in the following cases:
- water is not available or is too expensive;
- in the case of very dry environments, where water can create problems for production;
- with water-sensitive packaging.
Pasteurization and air-cooling spirals find easy application in these contexts:
- - traditional fruit and vegetable canning factories;
- - production of pasta, especially long pasta, to "stabilize" the product;
- - meat production;
- - convenience-food production;
- - savory and sweet baking;
- - chemical and parapharmaceutical industry.
Interested in a air water system?
Fill out and submit this form: one of our experts will contact you shortly to answer your questions.